
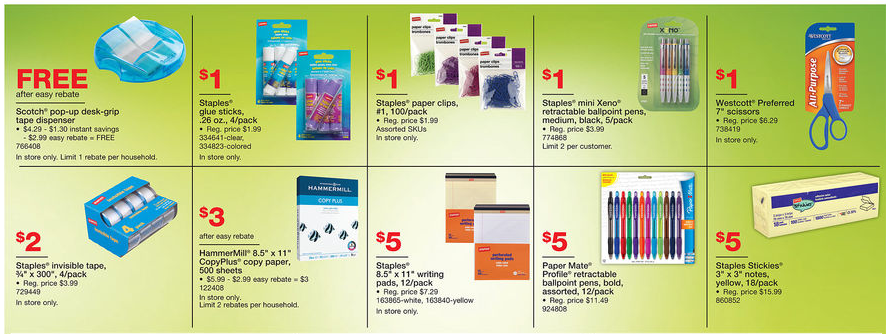
On a manual press, the squeegee performs this function. The ink is drawn across the image from front to back. Too high, too low, or an uneven gap will all distort the image, making multiple colors impossible to align. This spacing is known as off contact and is highly critical for the quality of your print. Once your substrate is in place, the screen is lowered and rests slightly above the surface of your substrate. In garment printing, this platen functions much like an ironing board. There may be a mechanism to secure the substrate, or it may be secure using spray glue. The substrate (what you are printing onto) is securely mounted directly below the screen. The equipment is ready, ink is on the screen, and you are prepared to pull your first print. The block out seals open spaces and pinholes so that only the desired design may print. Today’s emulsions are environmentally benign and require only water for processing.Īny areas on the screen where ink can pass through but are not part of the image receive a coating of block out product. Once the screen is exposed, the unexposed areas are washed out, leaving open mesh where your image will print. Again, this process requires highly specialized, costly equipment. This method saves time by eliminating steps and enhancing accuracy. Many busy commercial screen printing companies eliminate the film and use laser technology to create the image digitally. This step is most often done by placing a film positive of your design against the emulsion and exposing it with a high-intensity light source of a specific wavelength.Ī piece of equipment called an exposure frame performs this function.Ī vacuum firmly holds the film against the emulsion, allowing for precise translation of the design on the film to the emulsion on the screen.Īnother method of exposing the design onto the emulsion is Direct to Garment (DTG). Once this emulsion has cured and is ready to accept your design, the next step is to transfer your design to the screen. It can be accomplished manually, but this is highly sensitive to technique and takes much practice. The coating process requires specialized equipment designed specifically for screen printing. They require mixing and cure faster than diazo emulsions, but not as quickly as SBQ-based emulsions.A light-sensitive emulsion (photopolymer) is applied to the screen once it is properly stretched. Dual-cure emulsions are versatile and create very durable stencils. As a result, they are not as well suited to waterbased inks.ĭual-cure emulsions combine diazo and photopolymer emulsions. Pure photopolymer emulsions have long shelf lives, but most are not very water-resistant. These emulsions tends to create a thinner stencil, but multiple coats can be layered if a thicker stencil is required. The more delicate bonds created make them a good choice for detailed work. They are pre-sensitized, meaning that they are ready to use right out of the package with no mixing or other preparation required. SBQ-based or photopolymer emulsions expose within seconds, making them much faster than diazo emulsions. Once mixed, diazo emulsions will last a few months on the shelf. The resulting stencil tends to be thicker, making diazo emulsions a poor choice for detailed prints or prints that require halftones. However, diazo emulsions are less sensitive to light than other types of emulsions and require longer exposure times. Diazo emulsions change color during exposure, letting you know visually the degree to which your stencil is exposed. They require the manual mixing of photosensitizer with resins. The three main types of emulsions are diazo, SBQ-based or photopolymer, and dial cure.ĭiazo emulsions are a good choice for novice screen printers because they are affordable and easy to use. Ideal for beginners and great for busy artists, these all-inclusive kits make it easier to produce multiple copies of the same design.
#Screen printing staples vallum plus#
Shop for screen printing supplies and screen printing equipment such as inks, frames, screens, and machines, plus screen printing chemicals, apparel and other items to decorate, and screen printing kits. The resulting print is then dried or heat-set to cure the inks and set the design.īlick has everything you need for your next screen printing project. A squeegee is used to push the ink through the mesh screen one color at a time. For both photographic and non-photographic screen printing methods, one screen is required for each color being printed, and the screens must line up precisely to produce an accurate, cohesive design. Our Guide to Screen Printing Stencils provides more information on the three types of stencils used in screen printing. Screen printing is a technique that employs ink and mesh stencils to create vibrant designs on a wide range of surfaces and textiles.
